Why Use Metal Spun Components On Your Commercial Roof?
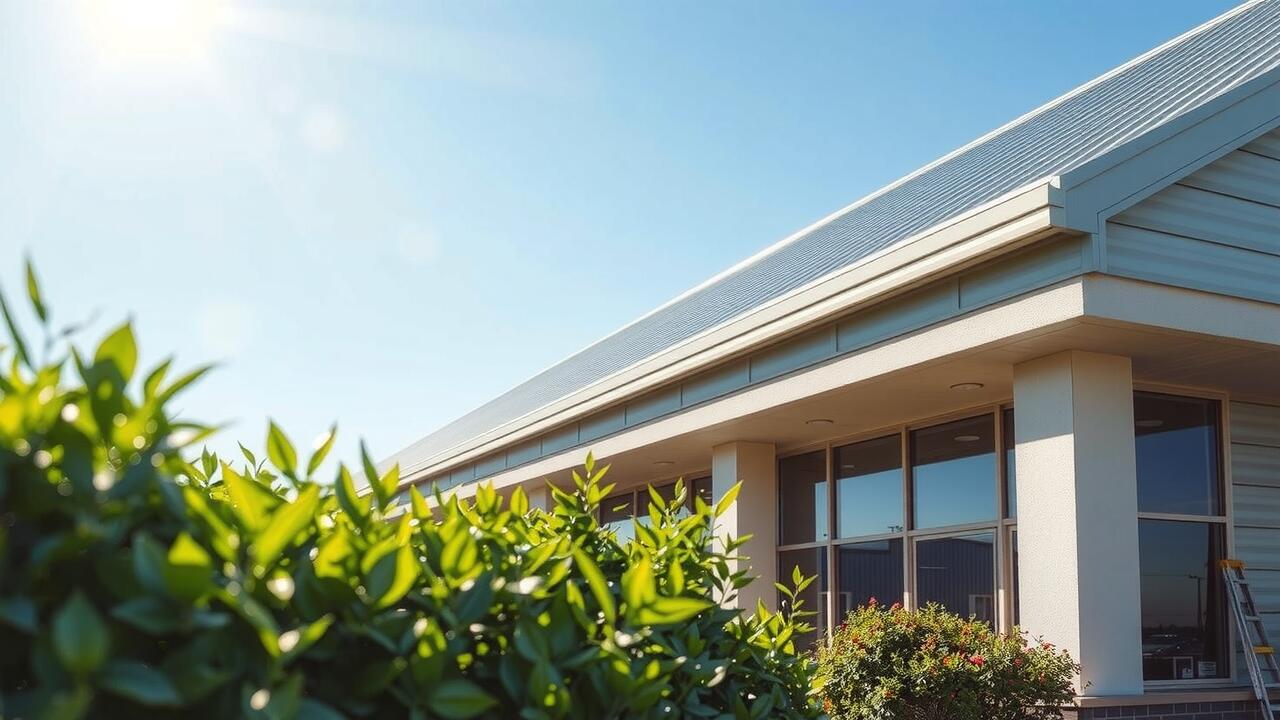
Table Of Contents
Comparison of Metal Spun vs. Traditional Roofing Materials
When comparing metal spun components to traditional roofing materials, key distinctions emerge in durability and adaptability. Traditional options like asphalt shingles tend to struggle under extreme weather conditions, causing concerns about leaks or wear over time. In contrast, metal spun systems provide enhanced resilience, particularly in regions prone to heavy rainfall or snow. Their superior design handles water flow effectively, minimizing potential ponding or runoff issues. Seamless metal drains exemplify this advantage, ensuring efficient management of excess water without the risk of clogs commonly associated with older materials.
Cost factors also illustrate significant differences between the two choices. While the initial investment in metal spun roofs may seem higher, their longevity can lead to savings in the long run. Traditional roofs often require more frequent repairs and replacements, escalating expenses over the lifespan of a building. Moreover, elements like vent pipe flashing add another layer of protection in metal roofs, further reducing maintenance needs. By embracing metal spun options, building owners not only enhance structural integrity but also streamline long-term performance—a compelling reason to rethink standard roofing solutions.
Key Differences in Performance and Longevity
When looking at performance and durability, metal spun components shine brightly compared to traditional roofing materials. Unlike asphalt or wooden shingles, which may warp or degrade over time, metal spun roofs offer exceptional resistance to harsh weather conditions. The design incorporates seamless metal drains that efficiently channel water away, reducing the chances of leaks and prolonging the lifespan of the roofing system. Think of it as upgrading from a bicycle to a sturdy motorcycle—you're trading fragility for strength and reliability.
Longevity takes on a new meaning with metal spun products, often outlasting other conventional options by decades. These components are crafted through a spinning process that enhances their structural integrity. Additionally, components like vent pipe flashing need minimal upkeep while providing excellent protection against moisture intrusion. Just imagine a roof that maintains its appearance and function long after traditional materials would have required replacement; that’s the practical advantage offered by metal spun roofing solutions.
Structural Advantages of Metal Spun Components
Metal spun components offer distinct structural strengths that make them appealing for roofing applications. Their ability to distribute stress evenly across the surface leads to improved durability. Unlike traditional materials that can buckle under pressure, the design of metal spun pieces enhances resilience. Take seamless metal drains, for example; their smooth construction eliminates points of vulnerability, ensuring water flows freely without risk of blockage or overflow. This can significantly reduce maintenance issues over time.
Weight plays a considerable role in roofing projects as well. Metal spun components possess a high strength-to-weight ratio that translates into easier installation and longevity. For structures that demand reliability, featuring vent pipe flashing crafted from spun metal can provide a seamless, flush finish that prevents leaks. These advantages not only contribute to a robust roof structure but also help in meeting stringent building codes. Choosing metal spun materials creates a solid foundation for any commercial roofing venture.
High Strength-to-Weight Ratio Benefits
When considering materials for commercial roofing, the high strength-to-weight ratio of metal spun components stands out. This property allows roofs to support substantial loads while minimizing the overall mass. For instance, roofs equipped with seamless metal drains benefit from lightweight structures that don’t compromise on durability. Think of it like packing your luggage—choosing lighter materials can lead to easier handling and better fuel efficiency, especially when transporting equipment to the site.
Durable yet manageable, these components significantly simplify the installation process. Vents for pipe flashing can also be constructed from metal spun materials, offering resistance against extreme weather without the added bulk of traditional options. Picture a sleek, modern building that not only meets the design expectations but also stands firm against harsh storms—this is the advantage of integrating metal spun components into roofing systems.
Expert Insights on Maintenance of Metal Spun Roofs
Maintaining metal spun roofs can be straightforward if you pay attention to a few important details. Regular inspections are key. Examine areas around vent pipe flashing for signs of wear or potential leaks. Over time, these critical points can be susceptible to corrosion, especially if debris accumulates around them. Addressing minor issues early can prevent more costly repairs down the line. Also, don't overlook the seamless metal drains. Ensuring they are clear of blockages is necessary for optimal water runoff and durability.
When it comes to cleaning, simplicity is often best. Use a soft-bristle brush along with mild detergent for removing grime without scratching the surface. This technique helps preserve the sheen of your metal roof. Additionally, consider checking the mounting hardware periodically. Loose screws or brackets can compromise the integrity of the roof, making regular maintenance indispensable. Keeping a close eye on these details ensures your metal spun roof remains functional and attractive for years.
Essential Care Tips for Optimal Performance
Taking proper care of your metal spun roof can greatly enhance its lifespan and performance. Inspecting your roof frequently is vital; look for signs of wear or damage around seams and at critical junctions like vent pipe flashing. A small leak can turn into a major issue if it isn't addressed promptly. Routine cleaning of the surface to eliminate debris ensures drainage through seamless metal drains remains efficient. This not only prevents standing water but also guards against premature corrosion.
It's wise to plan for periodic maintenance checks to address potential issues before they escalate. Consider applying protective coatings specific to metal spun materials. These treatments can guard against UV rays and other environmental factors. When it comes to repairs, embracing the same materials and techniques used in initial installation is key. This consistency will maintain the structural integrity of your roof.
- Inspect for wear or damage regularly, focusing on seams and junctions.
- Clean the roof surface frequently to remove debris that could block drainage.
- Schedule routine maintenance checks to catch issues early.
- Use protective coatings for added durability against UV rays.
- Employ the same materials and techniques for repairs as used in the original installation.
- Keep gutters and downspouts clear to prevent water buildup.
- Monitor interior spaces for signs of leaks or water damage.
Case Study
A notable project that highlights the efficacy of metal spun roofing involved a commercial complex in downtown Austin. The building’s owners were skeptical about traditional roofing options, primarily due to their tendency to degrade over time. After weighing various alternatives, they opted for metal spun components. The installation included seamless metal drains and vent pipe flashing, which ensured seamless integration into the existing architecture. The result was not just visually appealing; it also significantly improved the building's drainage capabilities, reducing the risk of leaks during heavy rainfall.
Another interesting aspect of this project was the collaboration with local engineers who praised the structural integrity of the metal spun materials. Unlike conventional roofing systems, which often succumb to the elements, the metal spun components offered unparalleled durability and resilience. This installation has since become a model for similar undertakings, showcasing how strategic choices in roofing materials can lead to long-term benefits. The owners reported a decline in maintenance costs, proving that sometimes, opting for a different approach pays off substantially.
FAQS
What are metal spun components?
Metal spun components are circular metal pieces created through a process where metal is spun at high speeds to achieve desired shapes and thicknesses. They’re commonly used in commercial roofing for their durability and strength.
How do metal spun roofs compare to traditional roofing materials?
Metal spun roofs usually outlast traditional materials like asphalt or shingles due to their superior strength and resistance to weather-related damage. They also tend to be lighter, which can reduce structural stress.
Are metal spun roofs more expensive than traditional options?
Initially, metal spun roofs can be more expensive upfront. However, their longevity and low maintenance costs often make them a more economical choice in the long run.
What are some maintenance tips for metal spun roofs?
To keep your metal spun roof in top shape, regularly clean it to remove debris, inspect for loose seams or fasteners, and apply protective coatings if needed to prevent corrosion.
Can I install a metal spun roof myself or should I hire a professional?
While some handy individuals might tackle a metal spun roof installation, it’s generally recommended to hire professionals. They have the right tools and expertise to ensure a proper and safe installation.